Home » 2025
Yearly Archives: 2025
The Importance of Dock Lifts
Dock Lifts is a great solution for areas that are frequently affected by rising and falling water levels. These semi-portable dock lifts mount on cradles and wear plates at the dock face, bypassing the need to form concrete pits or pads.
These units move vehicles from dock height (44.5-58″) to ground level quickly and easily. They can also handle truck impacts.
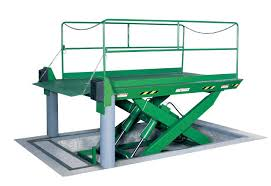
The dock lift is a crucial component of logistics in many industries. It bridges the gap between a warehouse or distribution center and transportation vehicles, improving efficiency and minimizing the risk of injury or product damage during transfer. Dock lifts also play a role in reducing the cost of truck or trailer equipment, which is typically passed on to customers. The best dock lifts are constructed of durable materials and have safety features to protect employees, customers and equipment.
When selecting a dock lift, you need to consider the maximum weight capacity that it can handle. This should be calculated by adding the weight of the cargo being transferred to the weight of the transport vehicle and the loader itself. You should also consider the platform size to ensure it can accommodate your largest loads and pallet arrangements. It’s important that your dock lift be easy to operate, with simple control mechanisms and clear visual markings to prevent accidents.
Additionally, you should consider incorporating safety systems such as interlocks and vehicle restraints that prevent trailer creep accidents. These safety measures can help reduce cargo spoilage, damage and theft at the loading dock. It’s also a good idea to include a communication system between drivers and dock workers that signals when a truck may approach the loading dock. This will prevent miscommunication and confusion and prevent unnecessary trailer movements.
Dock lifts that are in disrepair are an invitation for thieves to rob your facility. Make sure you invest in regular maintenance to keep them performing at their best and prevent costly repairs down the road. You should also consider adding barriers around the area to further deter criminal activity.
Efficiency
Dock lifts optimize loading dock operations by bridging the height difference between warehouse floor and truck bed, speeding up material handling, reducing manual effort and minimizing potential injuries. They also increase facility adaptability, allowing you to service a range of vehicle sizes and types beyond the traditional dock-to-truck transfer.
Whether used as a combination dock leveler / lift or a trailer lift, a dock lift is a safe and effective solution for facilities that lack an industrial loading dock or need to improve the safety of their existing one.
When selecting a dock lift, it’s important to consider its lifting capacity, vertical lift travel, platform width and length, as well as the method of operation. Most lifts utilize a NEMA 4 pushbutton control mounted on either straight cords or coil cords, which can be extended to allow workers to operate them remotely when they are not in use. In addition, many units have optional security features including key lock pushbuttons, which can be locked in secure boxes inside the building or secured with twist lock plugs and removed from the lift when not in use.
A dock lift can help to reduce the need for heavy lifting by workers, which minimizes back injuries and increases productivity. They also provide more versatility in the type of trucks and trailers a facility can service, reducing equipment costs.
The MobileDock Speed-Lift is a great example of a versatile portable dock lift that can be transported to a new location for loading or cross-docking operations without needing additional electricity or infrastructure like a pit. It’s ideal for emergency management, military operations, construction, agriculture, delivery and lumper services, city/county service centers and campus operations.
The DL Series Dock Lift from Blue Giant is another versatile portable dock lift that can be moved between locations and used for ground level cargo transfers in applications such as grocery stores, schools, hospitals and postal services, where a low-profile workhorse is needed. Unlike some other dock lifts, it can be set up on an uneven surface by simply adding locating cradles and wear plates. It is also designed to bypass the need for pit construction and can be lowered into a parking lot to facilitate truck-to-ground level transfers.
Versatility
Dock lifts bridge the gap between loading dock and truck bed during loading and unloading, improving efficiency, safety and product transfer. They are especially helpful in locations where docks do not exist, are improperly sized or the height of truck beds vary significantly. They allow a single piece of equipment to serve a wide range of trucks, from low step vans to high reefer semis.
Because they keep loads level, they make loading and unloading faster, safer and easier than ramps or steep inclines. They are also more efficient than tailgates, which require frequent operation and maintenance and can become obstructions to traffic. Whether you need to service a small fleet of vans or a large mixed-truck operation, a dock lift is an economical alternative.
When selecting a lift, consider the weight capacity of your typical loads and pallet arrangements. Look for lifts with simple controls that are easy to understand and operate. Choose a dock lift that is durable and can withstand the elements. If your location is in a rough water environment, look for reinforced arms, mechanisms and bolts for strength and protection against corrosion.
Depending on your facility’s needs, you may want to consider a dock lift with a remote power unit and weather cover for convenient servicing and protection. Choose a model with a maximum axle load slow-speed drive over rating, which refers to the amount of weight that can be driven over a fully lowered lift without damaging the vehicle or injuring an operator. Most recessed dock lifts are rated for 10,000-pound axle-load drives, while top of ground units can be adapted to higher capacities.
A recessed dock lift, like this Presto Trans-A-Dock, is a durable, easy-to-use solution for your facility’s truck access needs. With a lowered height of only 8 inches, this lift is more compact than traditional pit-mounted dock lifts. Plus, it can be easily moved if you need to relocate the lift in the future. And it doesn’t require a concrete pit or pad, which can be expensive to install and maintain over time.
Maintenance
Performing regular maintenance is vital for the longevity of your Dock Lifts. Checking the mechanical and electrical systems for damage or wear will help you identify issues early, allowing you to make repairs before they become worse. Additionally, a thorough inspection of the lift’s hydraulic system will ensure proper functionality and safety.
Keeping your lifts clean and free of salt and other environmental contaminants is also crucial to their lifespan. This will not only prevent corrosion, but it will also reduce the amount of maintenance required by the lift. For example, by regularly cleaning the structure of your lifts and applying a rust inhibitor or paint, you can prolong their life by up to four times.
Dock lifts allow you to transfer goods between the warehouse floor and trucks without requiring workers to do heavy lifting, reducing injury risk and enhancing efficiency. They’re also versatile tools that can accommodate a range of truck heights, making them useful for any shipping and receiving application. In addition, loading dock lifts are less costly than traditional tailgate lifts and can be used in a wider variety of truck sizes and types.
Inspect the cables of your lifts for signs of fraying or corrosion, and replace them as necessary to maintain their structural integrity. Additionally, inspect the pulleys and bearings of your lifts to ensure that they’re functioning properly. Lubricating these components with marine-grade lubricant can help reduce friction and extend their lifespan.
It’s important to periodically re-test the safety mechanisms of your dock lifts, such as the emergency stop functionality. This will help you identify potential problems and ensure that your employees can operate the equipment safely.
In addition, it’s a good idea to regularly take pictures of your dock lifts from different angles. This will allow you to compare them with previous pictures and spot any deterioration or damage that may need attention. It’s also a good idea to use anti-slip coatings on your lifts, as these will provide additional traction and help to reduce the risk of accidents. These coatings can be purchased in a range of colors and can be applied easily with a brush or spray.
Expert Plumbing and AC Solutions You Can Trust
An AC service technician can address any minor problems that may be occurring. For example, they can clean the air filters or check the condensation drain for clogs.
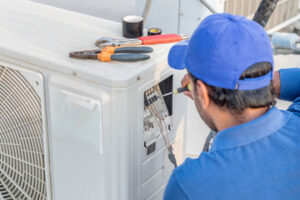
Whether you need to repair your AC, the experts at Got Flow Plumbing & AC Services can help.
A well-functioning air conditioning system does more than cool your home. It regulates humidity levels, filters allergens, and keeps your family comfortable. If you’re considering installing a new AC unit, call the experts at Bailey Plumbing Heating Cooling to get the job done right.
Air conditioners are complex systems that require extensive pre-installation inspection and assessment. During this process, an experienced technician will ensure that your new AC unit is properly sized, installed, and compliant with local building codes. This helps avoid premature wear and tear, energy inefficiencies, and safety risks.
The technician will also inspect the existing ductwork system to determine whether it is compatible with your new AC unit. If it is not, the technician will evaluate and make any necessary modifications to optimize airflow and maximize efficiency. This step will also help to identify any inefficiencies or issues that may impact the performance of your newly installed AC system, such as clogs or leaks.
Your new air conditioning unit will be mounted and connected to the ductwork, electrical, and refrigerant lines. All of these connections will be inspected and secured to prevent damage, short circuits, or improper operation. The technician will also verify that all electrical connections meet the voltage and amperage requirements of your new AC unit.
A well-functioning HVAC system is an essential component of a healthy, comfortable home. If your system is not cooling effectively or making loud noises, it’s time to schedule a professional AC repair or replacement service. Trust the AC specialists at Einstein’s to provide the quality home services you need in Park Slope and throughout Brooklyn, NY.
AC Repair
When you need AC repair, count on our technicians to quickly and efficiently solve your cooling issues. Whether you need to replace a worn-out air filter, clean the condenser coils or check the electrical components of your system, we can provide the solutions you need to get back up and running.
If your AC won’t turn on, it could be a simple issue like a blown fuse or an overloaded circuit. If that’s the case, flip the breaker switch to the “Off” position, then back to the “On” position to see if it fixes the problem. If it doesn’t, there may be a wiring problem that only an experienced professional can resolve.
An unwelcome odor from your AC may indicate mold development in the unit or its ductwork. This is a common problem that stems from poor airflow combined with high humidity levels. Fortunately, routine maintenance tasks like cleaning your AC drain line can stave off mold growth and help keep your home cool and comfortable.
AC Maintenance
The air conditioning system is one of the unsung heroes in your home, providing comfort during scorching summers. In addition to cooling, it also regulates humidity levels and filters out allergens for a healthy indoor environment.
The best way to extend your AC’s lifespan and ensure optimum performance is to maintain it with regular professional services. A routine maintenance appointment will check the status of your unit, including refrigerant levels and electrical connections. In addition, it will lubricate moving parts to reduce friction and help the system run more efficiently.
Many of these services are relatively simple for homeowners to perform, but others require the skills and tools of a certified technician. It is important to have an HVAC company you trust with your home’s air quality, comfort and safety.
Some of the most common issues that require a professional’s attention are:
Your AC system collects dust, debris and dirt over time, making it less efficient and impacting its ability to cool your home. Cleaning critical components like evaporator and condenser coils, air filters and drain lines can improve the efficiency of your system. In addition, your AC system can suffer from clogs in the condensate line and ductwork that compromise airflow. Getting these problems resolved quickly prevents damage and expensive repairs.
Another benefit of regularly scheduled AC maintenance is extending your system’s lifespan by identifying minor issues before they turn into costly repairs. A technician can inspect the system for signs of wear and tear, as well as tighten loose screws, lubricate moving parts and verify proper refrigerant levels.
Keeping your home’s temperature comfortable all year round is essential for your health and happiness. Whether you need heating or air conditioning repair, installation or maintenance, contact the team at Bailey Plumbing to get the job done right.
AC Replacement
The average air conditioning system will last about 10 years, but if you’re having trouble with yours, it may be time to consider upgrading to a new unit. Our technicians will help you evaluate your options and weigh the pros and cons of different cooling systems to find the right fit for your home.
Performing basic maintenance on your AC will keep it functioning properly, but for a more thorough inspection and tune-up, you should hire a professional. These services include cleaning the coils, changing the air filters, and checking refrigerant levels. Having these tasks performed regularly can prevent air conditioner problems and reduce your energy consumption.
A common air conditioner issue is clogged drain lines, which can lead to system malfunctions and even leaks. If left unchecked, this problem can escalate into a serious water damage issue that requires costly repairs. Our professionals can easily diagnose and fix your clogged drain line, saving you money and preventing serious damage.
Whether your plumbing, air conditioning, or heating is in need of repair, our team has the skills and tools to get it done. Our technicians follow a thorough and professional process to ensure that your home is comfortable and that you’re satisfied with our work. We’re committed to providing you with the best service, which is why we offer a 100% satisfaction guarantee. Schedule an appointment to learn more about our services!